Thought Leadership
How beneficial reuse of soil from construction can reduce your project costs and your carbon footprint
April 13, 2022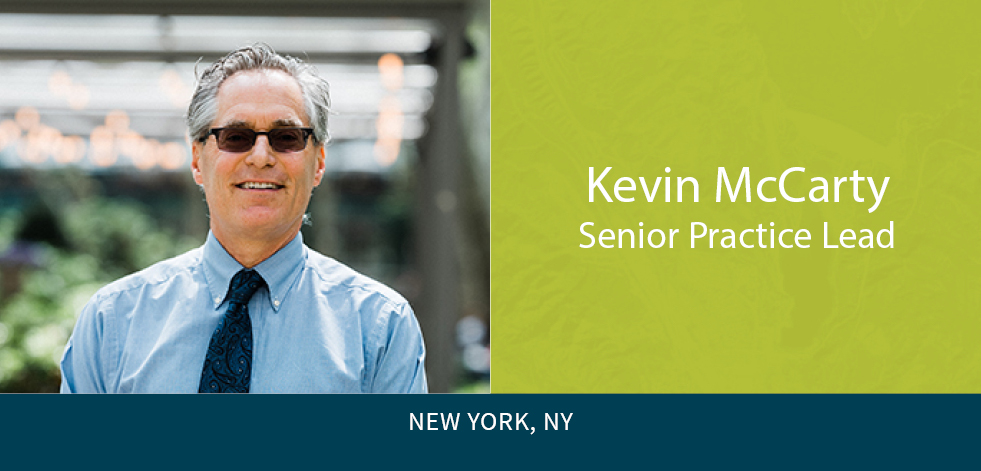
It is virtually impossible to build a structure, a building, or almost any type of fixed facility, without excavating ground and removing soil and fill material. Many projects require significant excavation for foundations, support structures, utilities, and ground improvements. It is also very common for the construction site to not have room to stage, store, or reuse material right away. This almost always necessitates off-site removal of all, or most of, the excavated material. If you have ever had a project that required moving a lot of dirt you know that, in many cases, the contractors you hire don’t put a lot of thought into how to handle it, they simply truck it out. But you will pay for that removal, which often includes tipping fees on the tonnage as well as high transportation costs when soil is moved out of State. Is there a way that soil can be reused? The answer is yes, and it could save hundreds of thousands or millions of dollars while, at the same time, improve sustainability. It just takes a little forethought and planning to make it happen. Let’s explore how.
In many areas, the regulations on moving dirt from a project site were written decades ago and have not been updated to account for the increased focus on sustainability and beneficial use. But those values have been filtering in. And as we strive for increased sustainability, the issue of beneficial reuse is gradually coming to the forefront.
Let’s consider a typical project. You have a design and your project specs have been determined. Unless directed otherwise, the contractor typically bids the job to include trucking away the excess dirt. At this point an engineer may take notice that if you test the soil, you might find it could be reused on another project. But the contractor isn’t invested in beneficial reuse because it wasn’t accounted for in the original job specs.
When beneficial soil reuse is built into the design, and the project specs are written accordingly, the owner gains the savings and the sustainability
In some cases, a consultant might be brought in to test the soil. But, too often, because this consultant was engaged after the design process, he or she will have little to no connection to the project. If the consultant doesn’t account for the parameters of the project (such as how deep will the excavation be?) the result is a generic report.
When this happens, you’re left without accurate data on the nature of the material to be excavated. Without that data, the engineer must guess at the quantities. And, if these estimated quantities are wrong, the contractor ends up issuing a change order. Enter the “dirt brokers.” In the states of New York and New Jersey, an entire organization of dirt brokers has popped up over the past 10-15 years. They parse out the dirt and are experts at controlling the flow of material to different locations and facilities, which makes justification for change orders much more effective. The cost and liability are then passed on to the owner.
So, what’s the solution to this wasteful, often convoluted process? We need to change how we think about the planning phase of the design process. When beneficial reuse is built into the design, and the project specs are written accordingly, the owner gains the savings and the sustainability.
Step 1: At the beginning of the design process, the environmental consultant, who will typically come in to assess the in-ground conditions that will inform the specifications and design, sits down with the landscape architect to gather the details. The environmental consultant will ask: What are you building? What will be excavated? Can any of this be retained for reuse on the project or is there no room for staging? How deep is the excavation? Once the consultant knows these details, or at least what the current version of the plan is, it’s easier for them to get some samples to determine what the fill layers are, where the natural material is, and then compare this to the existing criteria. The result? No wasted time on testing that doesn’t provide useful data. The consultant, now with inside knowledge of the project, can provide recommendations, including details on where fill begins and ends, as well as potential hazards. This information is very powerful and puts the owner in control of the process, rather than leaving it for the contractor during construction.
Step 2: Provide this accurate information to the engineer writing your project specs. Now you have precise data early, and the engineers can use this data rather than relying on guesswork. The result is that now the engineer can decide if the materials can be beneficially reused or if they need to be properly disposed of at facilities. You gain the advantage of the beneficial reuse simply by writing it into the specs, because that’s how the contractor bids it – no change orders necessary, and no environment harmed.
It’s a simple change to the process of thinking, really, with benefits all around. A process through which owners can save money and their sustainability teams can quantify the carbon savings is a win-win. When you account for the life of a construction project, these changes can save millions of pounds of carbon in just 4-6 months. And the cumulative sustainable carbon footprint reduction is astronomical when looking at dirt. The bottom line is this: When the owner has the specs written correctly, everyone wins.
To learn more about how to build beneficial soil reuse into your project, contact me: kmccarty@geiconsultants.com